Unilever’s commitment to energy efficiency and sustainability is enhanced by its advanced manufacturing facility located in Mannheim, Germany.
This site, famous for the production of Dove Bars, reflects the company’s dedication to technological advancement and environmental responsibility.
Originally established in 1899 as a small soap factory, the Mannheim facility has evolved into a vital distribution center for Unilever’s Home Care, Personal Care, and Beauty and Wellbeing sectors.
By incorporating innovative technologies and renewable energy sources in its manufacturing processes, Unilever achieves operational excellence while reducing its ecological footprint.
Emphasizing Efficiency and Sustainability
The Mannheim facility serves as a key component of Unilever’s global operations, linking four production sites that distribute Dove Bars internationally.
Utilizing sophisticated digital twin technology, Unilever has effectively interconnected these locations, facilitating real-time data sharing.
This integration not only enhances operational efficiency but also optimizes resource management.
A notable aspect of the Mannheim facility is its continuous automation and digitization, which significantly enhances overall equipment effectiveness (OEE).
An automated system monitors the production of Dove Bars along the assembly line, synchronizing this information with the supply of packaging materials. This meticulous tracking of inventory helps prevent production delays and increases efficiency.
Unilever’s sustainability initiatives are further underscored by its shift to 100% paper packaging for Dove Bars, which eliminates around 500 tons of plastic waste each year.
Moreover, the company has adopted solar energy solutions, demonstrating its commitment to renewable energy in manufacturing. These efforts reinforce Unilever’s dedication to environmental stewardship while upholding high production standards.
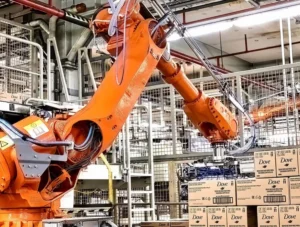
Utilizing Renewable Energy in Manufacturing for Sustainable Practices
The Mannheim facility plays a pivotal role in Unilever’s quality assurance initiatives, ensuring that Dove Bars adheres to international standards.
To further elevate quality control measures, Unilever intends to implement AI-powered cameras in 2025.
These advanced cameras will be capable of inspecting up to 800 bars per minute, thereby significantly enhancing production efficiency. By integrating artificial intelligence, Unilever reaffirms its dedication to providing exceptional products.
Marcela Melero, Chief Growth Officer for Dove Personal Care in North America, highlights the significance of these advancements:
“We are committed to creating undeniably superior products, and our Dove Beauty Bar exemplifies this. Unlike regular soaps that can deplete the skin of vital moisture, Beauty Bars are formulated with moisturizing cream to nourish the skin while gently cleansing away dirt and bacteria.”
An Exemplary Distribution Center
The Mannheim facility stands out not only as a significant production site but also as one of Unilever’s largest and most sophisticated distribution centers.
Initially a simple storage location, it underwent a remarkable transformation in 1999, becoming a state-of-the-art warehouse equipped with an automated management system.
This advanced system effectively manages inventory with minimal human involvement, thereby improving accuracy and alleviating logistical challenges.
With the ability to accommodate over 36,000 pallets, the facility oversees products from 30 manufacturing plants throughout Europe.
At its highest capacity, it processes 320,000 pallets each year, achieving an impressive customer case fill-on-time rate of 99.8%, which exceeds industry benchmarks.
To further enhance operational efficiency, Unilever intends to implement ‘layer picking’ automation by 2026. This enhancement is expected to boost picking capacity by 50% during peak times and yield annual savings of more than €1 million (US$1.03 million).
Factory Director Silvia Rissel emphasizes the company’s forward-looking approach:
“We are advancing digitization and integrating new technologies throughout our operations to improve productivity and expedite product delivery, all while maintaining the exceptional quality that our consumers expect. With initiatives such as plastic-free products, solar energy utilization, and apprenticeships aimed at nurturing local talent, the future of our Mannheim manufacturing site is promising.”
The Future of Renewable Energy in Manufacturing
As Unilever advances its digital transformation journey, the Mannheim facility stands out as a model of sustainability and operational efficiency.
The incorporation of automation, artificial intelligence, and renewable energy within the manufacturing process positions the company at the forefront of responsible production.
By emphasizing environmental stewardship and operational excellence, Unilever establishes a benchmark for the industry that others strive to emulate.
In the years ahead, Unilever intends to further enhance its sustainability efforts, concentrating on reducing carbon emissions, decreasing waste, and improving resource efficiency.
The initiatives undertaken at the Mannheim site serve as a template for manufacturing facilities worldwide, illustrating that innovation and renewable energy can coexist harmoniously in production.
Expert Editorial Comment
Unilever’s dedication to utilizing renewable energy in manufacturing for sustainable practices is reflected in every facet of its Mannheim operation.
From cutting-edge automation and AI-enhanced quality control to the adoption of solar energy and eco-friendly packaging, the company is committed to fostering significant change.
By prioritizing innovation and sustainability, Unilever guarantees that its products adhere to the highest quality standards while promoting a healthier environment.
As the company looks forward, it remains steadfast in its mission to establish new standards in responsible manufacturing.